Green Steel
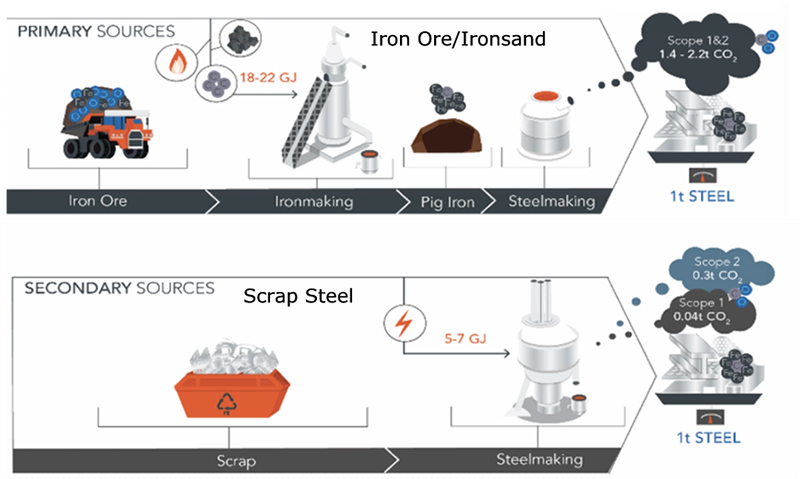
Is there such a thing? Isn’t steel, in spite of the fact much of our construction and much else relies totally on it, full of carbon and dreadfully unsustainable? Can it ever be “green” – which today seems to mean “carbon zero” (another catchphrase)? Isn’t use of steel always going to contribute to “climate change”?
Well there is a positive answer, and to look at it we need to dig into chemistry a bit. One of the first issues is the term “embodied carbon”. This doesn’t mean that the thing actually contains carbon. What it means is that carbon was emitted at some point in the process of making the thing, or may be emitted at some point during its life or end of life.
Building material alternatives.
Steel is used very widely in constructing buildings world-wide and is the largest material manufacturing industry. In buildings, steel is used for the structure (steel beams, girders, piles), as reinforcing for concrete floors and beams (rebar), and (our industry) in actually very low relative weights, as roof and wall cladding (and fencing and rainwater goods). Making it using current methods generates carbon dioxide (CO2 ) a potent greenhouse gas which has been shown to contribute significantly to global warming and climate change.
Looking at the two main alternatives to steel for building;
Timber contains a lot of carbon which has been removed from the atmosphere during the life of the tree in the process of growing the tree, from CO2 and sunlight (photosynthesis) – and water - by turning it into to O2 (oxygen) and carbon compounds in the structure of the tree. While the tree is alive this wonderful process is what creates the oxygen in the atmosphere which keeps all the rest of life living. Once the tree is felled this process stops and the carbon is locked into the timber and released only when the timber is allowed to rot (slash and site waste) or burned or buried, or at end of life of the building unless reused. The actual lumber contains locked in carbon – this is what I would call “embodied”; the proper term is “sequestered” meaning isolated or hidden, not removed. It does not absorb any more CO2.
Concrete is made using cement, one of the oldest manmade building materials. It is basically made by heating limestone (calcium carbonate) to high temperature in a furnace, which is often coal fired. This liberates CO2 leaving calcium oxide which combines with the other chemicals in the mix to form cement. Cement then used in making concrete is one of the largest generators of CO2 both from the chemical process and the use of coal to generate heat. The concrete industry globally is working on reduction of this embodied carbon with a variety of techniques, and success. Concrete in fact can absorb some CO2 during its life in a degradation process.
So timber during its creation absorbs carbon, and contains it for the rest of its life. Steel and concrete on the other hand both generate CO2 during the process of manufacture and do not contain very much carbon in the finished product. Whatever happens to the manufactured product, no CO2 is liberated either during the life of the product made from the material or after.
Since we are manufacturers and users of products made from steel (yes and some aluminium) we can discuss steel only, why it is or isn’t “green”, how it contains virtually no carbon, but creates CO2 during the current manufacturing process, and what we can do to make it “greener”.
Steel manufacture.
We have seen how concrete liberates CO2 into the atmosphere during the manufacture of its key material, cement.
The manufacture of steel also creates CO2 during the manufacture of its key ingredient, iron, from iron ore. Typically iron “ore” is found in the form of iron oxides or carbonate, but other forms exist as well in one of the Earth’s most common elements in the upper layers of the planet. Again typically (but not in New Zealand) this is in the form of rock located often far away from where it is to be used, even in a different country for much of the world’s use, and so also has a transport element of the total carbon footprint.
This is then crushed and processed into a form suitable for conveying (pellets), mixed with coal (or indeed other carbon containing materials like coke or charcoal) and heated in a furnace. The chemical process is quite simple – iron oxide + carbon (coal) becomes iron + carbon dioxide – which is released to the atmosphere as a greenhouse gas, and so contributing to global warming.
FeO (Fe2O3, Fe3O4) + C = Fe + CO2
The iron is subsequently converted to steel either in an electric arc furnace (EAF) or a basic oxygen furnace (BOF). An EAF typically uses a large proportion of scrap steel (or indeed 100%) to assist the melting process. This process removes the 5% odd carbon still left in the iron (as CO2 ) and reduces it to less than 1% for most grades. EAF which is primarily melting already made steel requires much less energy than the BOF process.
As you can see the conversion from iron ore liberates much more CO2 than just melting scrap, and most of the CO2 from EAF is from power use (Scope 2)
New Zealand Steel process
New Zealand Steel has a unique process for making steel which is probably more sustainable than any other – apart from using BOF not EAF. Instead of using rock-bound and distant iron ore, its source of iron is “ironsand” a material generated by historic volcanic action and containing a high proportion of magnetite (Fe3O4 ) as well as significant quantities of vanadium and titanium (sometimes called titanomagnetite). The surface mine is close to the steel mill, and cleaned and partly concentrated ironsand is transported by underground slurry pipeline the 20 odd kilometres to the mill, not hundreds or thousands of kilometres by truck and/or sea.
Here, it is, as with all current ironmaking, mixed with coal and heated in a rotary kiln to eventually produce molten iron This is then processed into steel using a blown oxygen furnace, into slabs of steel. This is made into a range of items, including the hot and cold-rolled high tensile steel sheet and coil which is the base for the products that we use to make cladding materials.
So while our New Zealand production is comparatively sustainable, using local raw material with high concentrations of oxide, and electricity made (mostly) from hydro-power, and with a enviable water cleaning system, it still produces steel with high “embodied” carbon created by the release of CO2 during the manufacturing process. NZ Steel remelts its own internal scrap during manufacture, but NZ’s “post-consumer recycle” – scrap steel after use in applications like cars, is now all processed overseas – and some of it may find its way back in products.
Globally the industry continues to create new iron from iron ore even though it is a more carbon and energy intensive process than recycling scrap for the simple reason that, partly because of ever increasing demand and partly because of the long life of most steel products before they become available for recycling, there is nothing like enough scrap available. About one-third of global production is remelted scrap.
Mitigation of embodied carbon.
There are a number of more or less significant methods to reduce the carbon footprint of NZ made and used steel. Listed by the industry are –
Minimising embodied carbon
• Recycling/reuse which extends the life, and of course steel waste during use is minimal and is all indefinitely recyclable.
• Operational efficiency improvements
• Sourcing energy from low carbon sources
• Carbon capture and storage/usage
• Improving subsequent steel processing
These minimising strategies are currently used in NZ and globally with varying degree of application and success, and can only go so far.
Removing embodied carbon
• Offsetting
• Finding an alternative reduction process
Only these two offer almost total reduction in the “embodied” carbon content of steel.
So, to looking at removing embodied carbon from steel. There are two routes currently possible; one is common to many industries and activities and the other is a new concept specific to steel.
Offsetting
This is not really removing the carbon content of your product, but buying some nominal relief. This process is in a way related to the Emissions Trading Scheme in that it does not physically remove carbon or prevent its generation, but seeks to buy offsetting – meaning to buy other carbon removing/reducing mechanisms to off-set the carbon you use or generate in your processor activity. You will be aware that when you buy an air ticket (which generates heaps of CO2 ) you can buy a carbon offset to overcome “flygskam” or flight shame. In New Zealand, Ekos (among others) offers carbon offsets by planting native timber. An example provided to Sustainable Steel Council by Thinkstep suggests that carbon offset cost for a typical house with a 0.40 mm steel roof is of the order of $35.
While it may seem ironical that NZ has gone from cutting down trees to make dairy farms to now planting trees on farmland to provide a CO2 sink. In order for this to last the trees should be mostly native, which are slower growing but much longer lived than pinus radiata.
So this is not really preventing CO2 from being released by the steel making process, just compensating for it.
Alternative reductant method
The only real method. As we have seen, the whole carbon problem with steel (really with iron) is that the current process (and that used since the Iron Age began some 2800 years ago) uses carbon in some form as the method for removing oxygen from iron oxide – by creating carbon dioxide. So, can we use something else to remove oxygen and leave iron, without using and then releasing carbon? One of the commonest (and cleanest) materials on Earth is water, which is H2O, a combination of oxygen and hydrogen (which just happens to be the commonest element in the Universe (but not found on its own on Earth unfortunately!). So can we use this and make the equation -
FeO (Fe2O3, Fe3O4 ) + H = Fe + H2O ? Well, yes we can, but the two devils are a) in the details and b) getting the hydrogen.
Hydrogen – there are currently three methods of producing this on the planet –
Grey hydrogen - derived from natural gas and fossil fuels, so available but releases lots of CO2, so this is not a solution. Blue hydrogen uses the same process as grey but captures the CO2 and stores it separately. This is not really a solution either.
Green hydrogen is made by electrolysis of water, and uses renewable sources of energy such as hydro, wind and solar power, all available and used in NZ.
So, the environmental advantages of green hydrogen are what we need to make steel, but producing this clean energy source currently uses more energy, if cleanly.
So we want green hydrogen, and NZ is a good place to make it with non-carbon based energy sources.
Obviously this process is up there with fusion power as the Holy Grail of carbon reduction. If we can really make steel with no carbon (not off-set into some trees, which will eventually get cut down), for such a large use globally, this would reduce global carbon emissions significantly.
What is happening.
In New Zealand the Robinson Research Institute, at Victoria University of Wellington, in collaboration with NZ Steel, is working on development of a pilot plant to produce steel using hydrogen as reductant.
In Sweden, the SSAB Hybrit project is producing a small amount of high quality steel from Swedish ore, using green hydrogen made using hydroelectricity, at the Lulea plant.
So - watch this space – and in the meantime, buy some off-set.
Green Steel – when not if.
Some reading/listening –