A WORK OF ART
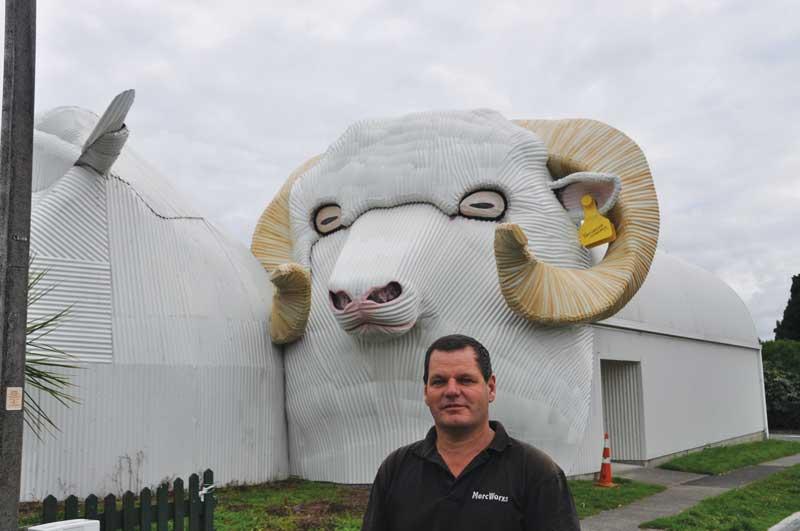
It takes imagination without limits, a personality stimulated by challenge, and a combination of engineering skills and experience to turn a utilitarian roofing material into an ingenious work of art.
Steven Clothier has been making iconic landmarks around New Zealand from corrugated iron since he built the Tirau Dog I-site in 1999. This started Tirau’s renaissance into the ‘Corrugated Capital of New Zealand’ and initiated an unexpected career path for Steven.
Demand for his skills in manipulating iron into art has become a full-time business for the qualified mechanic and multi-skilled handyman. He now has a full-time assistant and twin workshops, with the second 8m x 12m bay devoted to taking corrugated iron to forms undreamed of by its manufacturers. (The first bay is dedicated to his passion for Mercedes G-wagon modifications.)
Working only by commission, the three-man team (his wife does the administration) has constructed thousands of Creations. From the entrance signs at Wellsford and Warkworth, a huge range of corrugate work in Tirau and kiwis in Otorohanga, to as far South as the Whistling Frog in the Catlins...many are on public display though many more populate private gardens.
“The variety of our customer’s requests continuously amazes us – which is what keeps the job interesting”, said Steven. “We have no desire to churn out hundreds of the same things – though we can never make enough small pukekos for the garden. It is much more stimulating to build the largest pukeko in the world – and then try to erect it in a swamp in Otorohanga. Or experiment with different things to make a string of pearls on a stiletto-wearing pukeko for a jewellery shop in Tirau.” (He ended up using painted ball floats.)
An addition earlier this year to Tirau’s compilation was a six metre high Ram’s head adjacent to the Tirau Sheep. Originally commissioned by his brother and partner who were selling merino clothing in the building at the time, it had been a construction Steve thought would add to Tirau’s status. “We bounced around a lot of ideas. Originally they wanted a lamb – but how do you make a baby that needed to cover a building the same size as its ‘mother’? It would’ve looked like two-headed GE sheep. Then maybe a cow which would make a triptych.” Steve suggested a ram which he thought was the perfect solution – until he looked closely at a ram’s horn and realised how much work would be involved. “It certainly wasn’t one of those jobs you do for profit,’ he said wryly.
While the Dog is on a wooden frame and was constructed in situ, the Ram was built on a galvanised pipe frame in the workshop. “We have been using 0.40 gauge ZINCLAUME® corrugate from Roofing Industries for years but in this case I got them to corrugate some aluminium for me.”
Easier to curve into the tight folds that corner the triangular horn, Steven found the aluminium great to work with.
More recently a 4.5m high rooster wearing an Akubra cowboy hat has been constructed for a retailer in Brisbane.
“Australia has these huge pylon signs, and they are big, dominant and numerous on the street our customer is on – so we had to do something to make an impact and grab people’s attention. And of course, it had to reflect our customer’s business which is lifestyle farming and gardening supplies.”
The colourful rooster, now christened Ted, is certainly a landmark, but building for the other side of the Tasman presented its own set of requirements.
Shipping being a substantial portion of the final cost, the rooster was made to the maximum size that could be crated into a container. Three double-sided tail feathers and a front wing were removable, but able to slot into the internal pipe frame on installation and were packed down into a custom crate.
Internal pipe sleeves were built into the frame so the Rooster could be slipped over foundation poles – contrary to his usual practice of building the footings into the Creation itself. “It substantially reduces size and weight that way, which all saves on transporting costs, and made it easier for them to comply with and sign off on the Australian legislation regarding installation.”
Even so, total weight of the Rooster in the crate was 578kg.
Corrugated iron has long been embraced by New Zealanders for versatility and Steven has taught himself numerous ways to work it to get the effect he wants. Baby iron, layered pieces, curved iron, kinked iron – it is all cold cut with a nibbler and riveted into place.
“Once we turned up to install a sign the owners wife had ordered for his brand new million-dollar building but there was no way he was letting us go near his new shed with a drill. Once we explained our construction process and assured him that our Creation would last as long as his shed, he was OK. We have confidence in our product and in our methods.”
But that definitely has its pluses and minuses, the Creation can outlast the business or building owner with the new owner modifying their Creation into something quite different, but it is still credited to Corrugated Creations.
“We sometimes cringe as we drive past a 15 year old piece we have made covered with moss and bird droppings or repainted in a way different from ours. But what can you do? I am sure artists who work with more temporary mediums never have this issue.”
Personally, Steven would prefer to leave most of his Creations unpainted. “It shows the texture of the workmanship – the cutting and riveting, and the character of the ZINCALUME® itself.” Something he obviously appreciates as he clad his home and workshop in ZINCALMUE®. But as most of his work is large and viewed from a distance, and his customers want colour so roofing paints are applied for impact.
They have been surprised at the number of repeat customers. Private customers come back for more or purchase for family members, and business customers open more branches or new enterprises. Also the relationship they establish. Schools often get involved with the design process or come and see, and ‘help’ with, the construction, and Steve’s favourite customer still drops him in a chocolate cake on a regular basis.
Something, he admits, earns her a pretty good discount.
“Sometimes I wish I had another 100 hours in the week so I could indulge myself and build some of the concepts in my head,” said Steven. “But at the end of the day we get a huge sense of satisfaction out of producing for the customer something that fulfils their needs, and a Corrugated Creation that (hopefully) exceeds their expectations.