Nga Kereru in Maraetotara: A Strawbale House
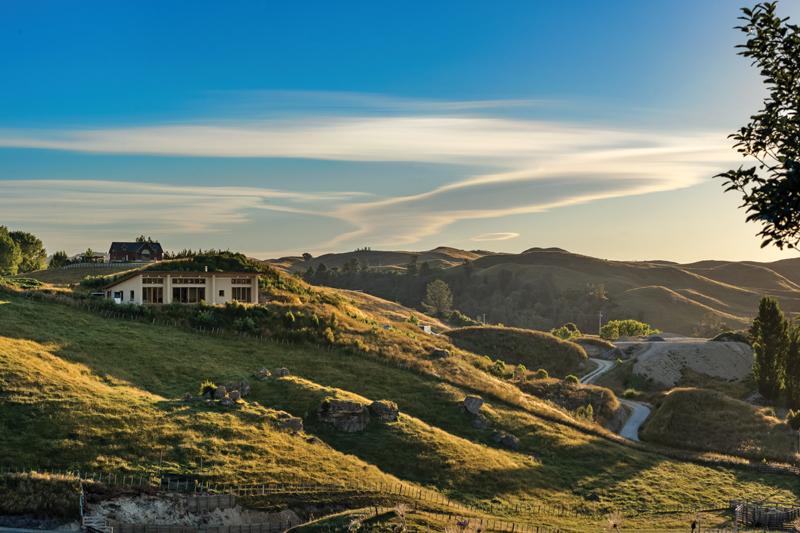
Nga Kereru in Maraetotara, Havelock North was purchased in April 2016 by Andrew Tuck and Alessandra Menegon with a dream to develop a rural sustainable lifestyle. The couple were living an international life in Australia and Europe and wanted to settle back in NZ and create a more sustainable building and lifestyle.
The name Nga Kereru is aspirational and reflects the native forest regeneration planting programme started in 2017, with 2500 local native trees and shrubs which attract and support many native birds, planted so far at Nga Kereru. Nga Kereru is within the cape to city native bird corridor in the Maraetotara river valley. The Kereru is New Zealand’s native wood pigeon.
As the concept developed to build a strawbale house with passive solar elements, the hunt was on for Alessandra and Andrew to find an architect and builder. After much deliberation and a few lucky connections, Alex Grieg from GreenHaus Architects and local builder Pat Mawson from Straw Home Hawkes Bay (www.strawhome.co.nz) joined the project team.
Pat Mawson is the current president of the New Zealand Earth Building Association. With over 10 years experience in straw and earth building. Greenhaus Architects has a philosophy that is based on the ecological building and design principles of the Building Biology and Ecology Institute and has been involved in several strawbale houses in NZ. Much of the initial design was done remotely with Alex in NZ and Peru, Andrew in England and Pat in NZ so with the help of Archicad 3d visualisations, Pat, Andrew and Alex were able to develop the design for Nga Kereru.
The site developed with services and connections being installed, taking advantage of the natural spring on site. By October 2018, Alessandra had moved to join Andrew in NZ and building consent was approved. Earthworks started for the caravan site, container site and the building platform and it felt momentous to finally being starting the build after so much dreaming and preparation.
The couple’s detailed forward focus and experience in project planning saw them making early decisions on appliances and other fixtures and this saved time and costs as they were able to be 100% clear on the layout for the plumbing of the slab, electrical design and so on. Using ex demolition kitchen and pantry carcasses aligned with the sustainable building culture of the project.
The design team chose Kliplok® as a concealed clip fixed roof that offered visually clean lines and low long term maintenance. Made in Colorsteel®, Kliplok® Flaxpod® is safe to harvest rainwater. The extra long flashings were supplied by local supplier Stratco. The roof faces south to allow for maximum passive solar gain through the north facing windows. Solar panels will be incorporated at a later date in a ground or roof mounted installation.
Having the roof on meant protection from rain and so the straw bales for the walls were able to be delivered and stored under cover inside the house. Organising and confirming the supply of straw bales was nerve wracking as the quality of the growing season could impact heavily on the availability of straw bales and therefore the build process. Fortunately it was a bumper season in 2018-2019 and supply was found for 320 bales of barley straw from Matapiro Station, an hour’s drive away.
Pat’s experience in straw bale house building came to the fore with the creation and installation of moisture meters - a simple way of setting up a base line for conductivity inside the finished walls.
The moisture meters allow early warning of any issues and help give the consenting authority confidence. They would normally read around 8 - 12%. Moisture content of the straw would need to be well above 20% for a sustained period to support fungus and rot. The moisture monitors will be re-checked in the years ahead to monitor any significant changes inside the plastered walls. The response to finding raised moisture levels would be to identify the source of the moisture and ascertain how complex the fix may be.
As the strawbales walls are the outside walls and the internal framed walls, by design, hold all plumbing fixtures etc, it is not very different from a conventional building in terms of identifying and resolving any issues with moisture. Ideally, strawbale houses are not sealed with Latex paint or cement render and this keeps the building open and makes it easy for moisture to escape. In Pat’s experience, even a flood resulting in 40% moisture levels in clay plastered straw walls dried out naturally, without need for intervention, returning to acceptable levels within a fortnight.
Family and friends and other locals who were on their own journey in straw bale building, joined together for the traditional wall raising where the straw bales are cut, laid and compressed into the house wall. In about 4 working hours they had completed raising the exterior walls – definitely a case of many hands making light work.
The strawbale walls were built using timber frame “bucks” with strawbale infill topped with a perimeter plywood/timber box beam. The height of the beam is set so that the bales will be a tight fit and well compressed. The first 4 bales were fitted, hydraulically compressed using jacks and then stropped in place. This created space for the 5th bale to be inserted into the wall in a tight friction fit and the strops were then released.
The external 450mm thick strawbale walls were plastered with a 35-40mm base coat of clay plaster on both sides. The final lime plaster finish on the exterior is more durable and resistant to erosion and rain. The internal clay plaster finish is easier to work with than the exterior lime finish and has reported health benefits in terms of humidity control, is negatively charged and releases no toxins. In addition to the natural beauty, the plaster system is a great insulator for heat/sound, it is airtight but allows vapour to move in/out of the walls and last but not least it also adds to the thermal mass of the house. Repairs to the interior clay plaster and exterior lime plaster finishes are simple and Pat leaves his owners with a manual so they can affect any repairs that may be needed.
As the plastering work started, Pat’s skills as a practitioner for clay and lime plaster systems in NZ were invaluable. Sourcing the clay from a local properties and hydrated lime from a local quarry maintained the connection with the land and minimised the embodied energy of these materials. Mixing mud for the plastering process is very labour intensive but was aided by the use of a plaster mixer/pump.
The house build has also established a canvas for art work. The first art installation was the creation by Alessandra and her friend Vicki Campbell of a beautiful stylised cabbage tree cob relief on the western wall that greets all visitors to Nga Kereru.
As the exterior clay plaster on the straw bale walls continued to dry, Thermadura shipped in all of the passivhaus certified timber exterior joinery, high performance glass and hardware from Germany and assembled it in their Mosgiel factory in New Zealand, before delivering it to the house site. Nga Kereru was built to the passivhaus principles of comfort all year round, energy efficiency and quality assurance and so the European profile, tilt and turn solid wood, high spec (U and R value) glazed doors and windows were critical for the house design to work.
The design brief tested the limits and the sliding door units are the tallest ever built by Thermadura, and the overhead windows are top instead of bottom hung to provide for maximum opening with the ceiling raked at 25 degrees. The team at Thermadura supported Nga Kereru every step of the way with good advice, clear boundaries on what was and wasn’t possible and then delivering on quality. The large slider frames were manhandled into place rather than hoisted to prevent damage to the frames, and Vitali from Thermadura then glazed and these units on-site.
Whilst the exterior of the house was being plastered, Terralana wool ceiling insulation was being installed in the ceiling to provide an R8 insulation rating. Being an organic material, Terralana helps store moisture from inside the house until it can evaporate off at a later stage.
The ply ceilings have industrial style exposed nail heads, which means a lot of time and care was taken in marking and then neatly nailing them off. The design of the west of the house incorporated a diaphragm ceiling with a huge number of nails, for example to put up just 1/3rd of the garage ceiling more than a thousand nails were used - there were some harsh words from time to time for the engineers who specified the nailing pattern.
The addition of wing walls to the front of the house and closing it in with the exterior cladding transformed the look of the house.
The wing walls are a mix of form and function; they break up the front of the house, providing some degree of privacy (or a least the feel of separation) and they help manage unwanted solar gain on the north facing glazing from the morning sun (east) and most importantly evening sun (west) in the summer months without significantly effecting views or reducing desirable solar gain in the winter months.
With great teamwork from the builders Pat and the RM strawbale team of Nils and Everett and the other trades, Bob and Geoff on electrical and Kenny (NZ master plumber of the year 2019) by July 2019, Andrew and Alessandra were able to move from their on-site caravan into the self-contained B&B flat within the main house - just 10 months from first breaking ground! Work progressed on completing the remainder of the house and they were able to move into the full house in October 2019. The oiled plywood soffits were finally added (the soffits were left to last to prevent marking from over spray from plastering the walls) and the cabbage tree artwork on the western wall of the house, inspired by another of Pat’s strawbale home builds, looks fantastic with its lime plaster finish coat.
The passive solar design developed with Alex from GreenHaus Architects has worked well in practice. The Northern soffits were designed with a 25 degree angle which is an extension of the interior ply ceiling as though it had swept through the walls and carried on out of the house. The 25 degree angle is the angle of the mid-winter sun at midday, so maximising the passive solar heat gain inside the house in the cooler months. The big, almost 2 metre, eaves on the North of the house allows for the angle of the summer sun, minimising passive solar heat gain inside the house in hot weather. In summer, cooling the thermal mass at night keeps the house cool during the day.
At the time of writing this article, the house build has just been completed including the kitchen with its beautifully recycled cabinetry and refurbished mismatching chairs, the sgrafitto moon-kereru artwork in the main bedroom and the sgrafito and linseed oil toe toe in the toilet.
Final finishing work on the exterior is being completed, with the front decks now built and landscaping around the house and restoration of the driveway underway.
The view from the main entry pathway of the rear deck and pizza oven is inviting, and this entertaining area was put to hard work with various celebrations during the course of the project, and creates a relaxing place to enjoy a quiet evening’s relaxation with friends.